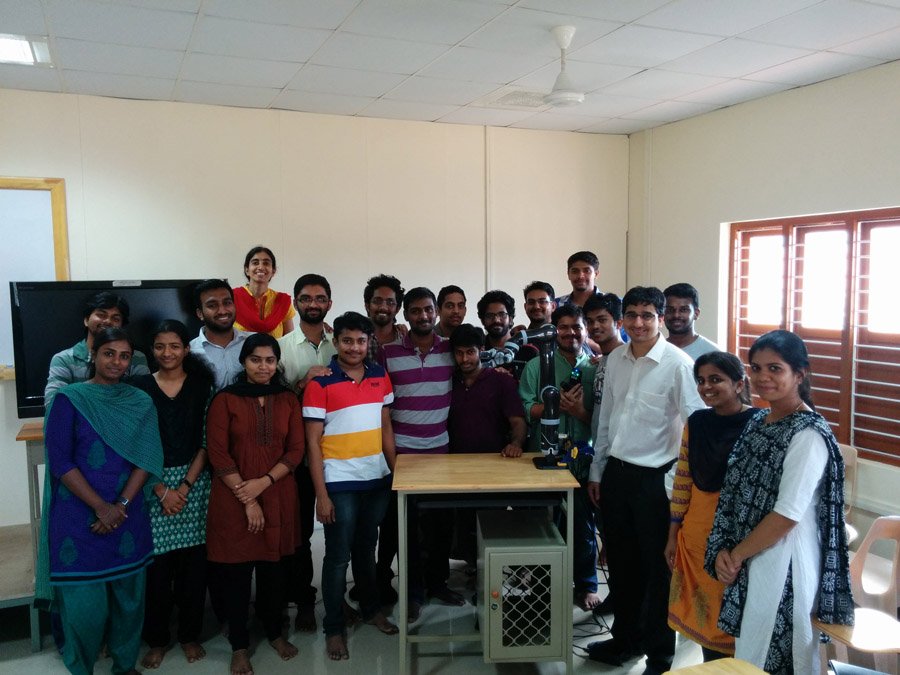
JACO² 4 DOF
JACO² 6 DOF
JACO² 7 DOF
GEN3 LIGHT ROBOT
Sensors
Computers & Networking
Controllers
All Accessories
3 kg (at 11.1V)
378°Per Second
5 kg with mouting base
11.1V 12.0V
Pose Repeatability
Maximum Velocity
Santulan Parallel Platform is a strong and agile 6-Degrees of Freedom parallel platform with a wide workspace. It is best suited for gaming integrations, precisely controlled manipulators, camera mounts with exceptional peep features, medical applications, 3D and 5D printing machines, laser cutting/engraving, and academic or research labs.
In the inverted mounting configuration, it can handle a wide range of food products, and can easily do pick-and-place operations as in the pharma, and electronics industry.
Type | 6-RSS Parallel Platform, 6DOF |
Number of axes | 6 |
Pose repeatability | ±0.173 mm (ISO 9283) |
Weight | 5 kg with mouting base |
Cubical workspace | 60mm × 60mm × 60mm\ |
Max Displacements | X ~ 320mm, Y ~ 308mm, Z ~ 158mm |
Max Angular Displacements | Roll ~ 43°, Pitch ~ 25°, Yaw ~ 65° |
Payload | 3 kg (at 11.1V) |
Operating temperature | -5°C to +80°C |
Mounting position | Floor, ceiling, walls, floating |
Size | 300mm × 300mm × 450mm with a Supporting Base Stand of 50mm. |
Surface finish, paintwork | Base stand (stationary) Metallic gray, Moving parts: Chromium-plated |
Material | Body – Chromium-plated mild steel |
Actuators – Engineering plastic body | |
Links – Mild Steel Coupler | |
Bolts – Stainless Steel | |
Joint Level Accuracy | 0.088° |
Minimum Incremental Motion | 1.5mm |
Maximum Velocity | 0.5m/s |
Maximum Joint Torque | 5.5N.m (at 11.1V) 6.0N.m (at 12V) 7.3N.m (at 14.8V) |
Maximum Joint Speed | 378°Per Second |
Force/Torque Control | Torque control (up to 10-bit precision) at each joint allows end-effector force/torque control |
Sound Level | < 50dB |
Top Platform | Modified for more agility and lightweight. Provision for mounting sensors and gripper |
Operating Voltage | 11.1V 12.0V (Recommended) 14.8V |
Maximum Current | 30A at Full load |
Standby Current | 600mA |
Connecting Cable | Single 3-Wire cable for Communication and Power |
Actuator Characteristics | Full metal gear PID adjustable using separate |
Actuator GUI Contactless absolute encoder (12 bit for 360°) | |
Feedback: Position, Temperature Position, Velocity, or Torque Control | |
Power Supply | 110/220 V to 12V |
Supported platforms | PC with Mac or Linux (Ubuntu, Debian, Raspberry Pi, or other distributions) |
Programming Compatibility | MATLAB, Python, Java, C/C++, C#, LabView, ROS. |
Communication | USB to TTL (Daisychain – Half duplex Asynchronous Serial Communication) |
API Compatibility | Python, ROS |
+ Cartesian Jogging for Position and Orientation
+ PTP Motion using Cycloidal, Cubic, Quintic, and Cosine trajectories
+ Controllers: Virtual using mouse, Android App or 3D Joystick
+ Programmed motions: Planar/Vertical SHM, Spiral, Lissajous, Helical, Precession
+ Live plot for joint angles for any cartesian motion, end-effector homogeneous transformation matrix, error logs
+ Mouse interactive 3D visualization and standard views buttons
+ Trace feature for end-effector motion visualization
+ Inbuilt safety feature for singularity check and joint angle limits
+ 1 No. all rotary parallel Stewart platform with actuators and base stand.
+ USB to TTL converter for communication.
+ 12V, 30A power supply.
+ Junction box with Emergency stop.
+ 3 core, 10m, submersible cable.
+ USB Drive with Software, API, Assembly Instructions, User Documentation, Android Application, Videos, and Example codes.
+ Lab Manuals for teaching.
Standard computer with i5 procesor or above, 8 GB RAM, with Graphics card. Preferably with Linux Ubuntu 14.04 or higher.
+ As a Laboratory Apparatus or in Classroom for Demonstrating Parallel Robot.
+ Positioners for Cameras, Solar Plates, Mirrors, and Surgical Instruments.
+ Motion Platforms: Simulators, Gaming Stations, Medical Applications, Test Workbench.
+ Torque-controlled joints allow it to be used as a Haptic Feedback Device or as an Assembly Robot.
+ Low-Frequency Vibration Compensators or Dynamic Balancing.